The Synergistic Power of Precision Manufacturing: CNC and Friction Stir Welding Empower the Innovation of New Energy Vehicle Battery Boxes
In the rapid iteration of new energy vehicle (NEV) technology, the safety and efficiency of power battery systems have always been at the core. In pursuit of higher energy density, better structural efficiency, and more reliable protective performance, the integrated battery box for NEVs has become an important evolutionary direction for the industry. These integrated designs pose stringent challenges to manufacturing processes: they require both millimeter-level precision machining and the high-strength, defect-free connection of large aluminum alloy components. The deep collaboration of CNC and friction stir welding provides solid technological support for this purpose.
CNC: The Precision Cornerstone for Complex Components
The starting point for high-quality battery boxes lies in the precise manufacturing of individual components. Computer Numerical Control (CNC) machining technology, with its exceptional repeatability and ability to handle complex surfaces, takes on the task of precision forming of key structural components. Faced with components in the battery box such as end plates, frames, and cooling plate interfaces—which often have irregular contours, thin-walled features, and high-precision mating surface requirements (such as flatness ±0.1mm, positional accuracy ±0.05mm)—CNC machining demonstrates irreplaceable advantages. With high-rigidity machines and multi-axis, coupled with specialized tool path planning, it can stably and efficiently complete three-dimensional surface milling, deep hole machining, and high-precision thread cutting operations. This precise control of dimensions and geometric features not only ensures the functionality of the components themselves but also provides a reliable matching benchmark for subsequent high-quality connections. Particularly for aluminum alloy materials driven by lightweighting needs, CNC is the key means to balance complex structures and surface integrity.
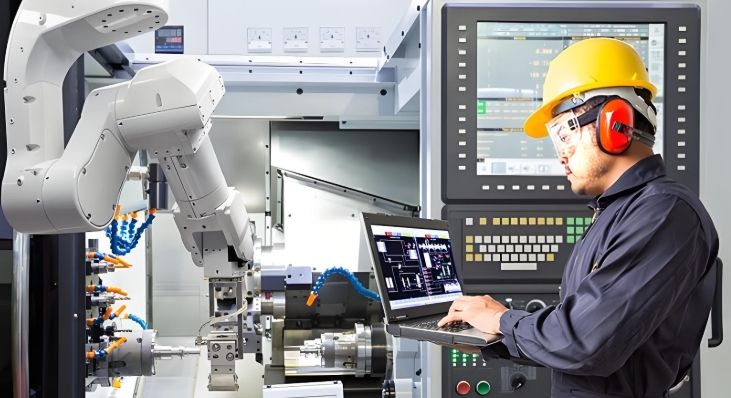
Friction Stir Welding: Robust Guarantee for Integrated Connections
When precisely machined components need to be integrated into a robust and sealed whole, traditional fusion welding methods often encounter bottlenecks in aluminum alloy applications: issues such as sensitivity to hot cracking, high porosity, significant welding deformation, and softening of the heat-affected zone frequently arise. The advent of Friction Stir Welding (FSW), with its unique solid-state joining mechanism, has opened up new pathways for the manufacturing of large integrated battery boxes for NEVs.
This technology utilizes a high-speed rotating pin tool that is inserted into the butt or lap joint seam. The material is brought to a thermoplastic state through frictional heat rather than melting. Under strong forging pressure and the vigorous stirring action of the pin, the interface material undergoes intense plastic flow and thorough mixing, forming a dense, fine-grained metallurgical bond zone. The entire process occurs below the material's melting point, fundamentally eliminating fusion welding defects such as porosity and solidification cracking. The extremely low heat input significantly reduces welding stress and distortion, while also avoiding excessive softening of the heat-affected zone. For key long weld seams such as battery box body splicing, frame integration, and cooling channel sealing, friction stir welding can stably provide joints with strength close to or even reaching the base material level (typical joint efficiency >95%), low residual stress, and excellent sealing performance.
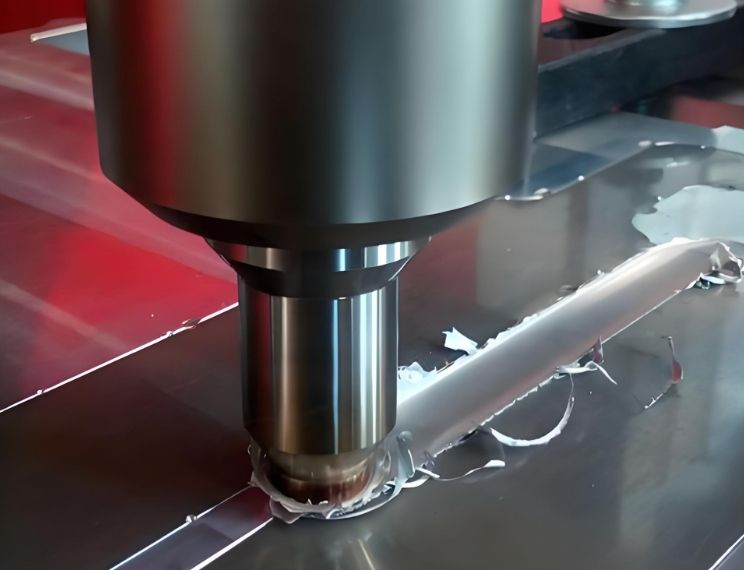
Synergistic Manufacturing Chain: Deep Integration of Precision and Strength
The high performance of integrated battery boxes for NEVs essentially relies on the seamless integration and deep collaboration of two core processes: precision forming with CNC and solid-state joining with friction stir welding.
-
Front-end Precision Assurance: CNC technology strictly ensures the machining accuracy and surface condition of each individual component. Precise geometric dimensions, strict tolerance mating surfaces (such as flange surfaces), and optimized welding bevel designs directly determine the joint quality and process stability of friction stir welding. A qualified friction stir weld seam begins with a qualified CNC-machined part.
-
Back-end Efficient and Reliable Connection: Utilizing friction stir welding to efficiently integrate the precision components machined by CNC into large integral structures. Its value lies in: completely avoiding the risk of fusion welding defects, ensuring structural strength and sealing integrity; minimal welding distortion reduces the amount of subsequent reshaping work or even eliminates the need for reshaping, ensuring the flatness of critical assembly surfaces; significantly shortening the cumbersome assembly process required by traditional riveting or bolted connections.
-
Performance Synergy: The resulting integrated battery box for NEVs achieves the optimal balance between structural rigidity and lightweighting, greatly improving internal space utilization, and ensuring the long-term operational safety and durability of the battery system with defect-free connections. This process combination also brings about the optimization of material utilization and an increase in production cycle time.
Precision CNC machining and reliable friction stir welding together form the advanced paradigm for the manufacturing of core components in modern NEVs. They represent the mature integration of precision manufacturing and high-quality joining technologies. In the production practice of integrated battery boxes for NEVs, the continuous application and optimization of these two technologies not only meet the current stringent requirements for performance and safety but also lay a verifiable manufacturing foundation for the further development of future power battery technologies. Their core value lies in transforming design intent into safe, reliable, and high-performance physical products through rigorous process control and assurance.