The Cornerstone of Chip Precision Manufacturing: Micro-Scale CNC Machining Beyond Limits
Constructing the computational cornerstone of modern civilization at the micro scale, the manufacturing process demands a level of precision that far exceeds conventional industrial imagination. As chip designs grow increasingly complex and packaging density escalates geometrically, the precision metal components that support their creation—heat sinks, lead frames, test sockets, vacuum chambers—become invisible barriers to performance and reliability. Traditional machining methods are showing their limitations in this domain, while the in-depth innovation of Computer Numerical Control (CNC) technology is injecting decisive power into the precision foundation of chip manufacturing.
Process Breakthrough in the Micron World
The manufacturing of chip-level precision components represents the ultimate challenge for engineering technology at the micro scale. Geometric dimensions are often measured in micrometers, with form and position tolerances as strict as a fraction of a hair's width, and surface roughness requirements approaching a mirror finish. More severely, the materials are often high-strength alloys, ultra-high thermal conductivity metals, or special engineering ceramics, which have a significant tendency to work harden and are extremely difficult to control for thermal deformation. Traditional machining methods often encounter bottlenecks in efficiency, precision, and consistency when dealing with the complex three-dimensional curved surfaces, micro fine deep holes, and ultra-high precision thin-walled structures of these materials.
Precision Empowerment of CNC Technology
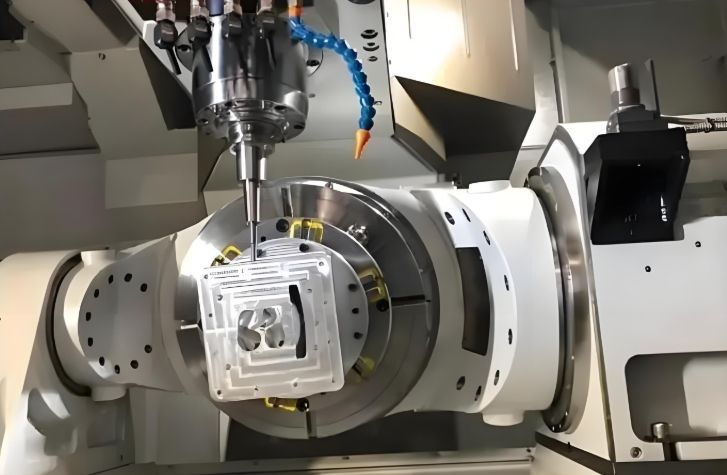
Modern multi-axis CNC machining centers, integrating ultra-precision motion control, intelligent temperature compensation algorithms, and adaptive cutting strategies, have become the core tools for breaking through the barriers of precision component machining in chip manufacturing:
-
Nano-level Motion Accuracy and Dynamic Compensation: High-performance linear motor drives, combined with high-rigidity mechanical structures and laser interferometry feedback systems, achieve true path control with nanometer-level resolution. Minute thermal deformations caused by environmental temperature and humidity fluctuations are dynamically corrected by the system's built-in real-time compensation algorithms, ensuring absolute fidelity of the machining trajectory at the micro scale.
-
Multi-axis Synergy for Complex Curved Surface Forming: The five-axis联动capability is key to machining complex curved surface components (such as irregular heat sink teeth, curved chambers, and microfluidic channels) in chip manufacturing. Through the CNC system's precise synchronous control of the rotary axes, the tool can continuously cut with the optimal posture, completing the machining of multi-faceted geometric features in a single setup, avoiding cumulative errors from repeated positioning, and significantly improving the contour accuracy and positional consistency of complex structural components.
-
Intelligent Process Strategies for Difficult-to-Machine Materials: For special materials commonly used in chip manufacturing, such as oxygen-free copper, molybdenum copper alloy, and silicon carbide-reinforced aluminum-based composite materials, the system integrates an intelligent process database. Through the adaptive control module, based on real-time feedback of cutting load, the system dynamically optimizes the spindle speed, feed rate, and cutting depth (such as using high-frequency micro-stepping milling strategies), effectively suppressing work hardening, abnormal tool wear, and cutting heat accumulation, ensuring sub-micron dimensional stability of fine structures on high-hardness materials.
-
Full-Closed Loop Quality Assurance System: Integrated online measurement probes (contact and non-contact laser types) automatically perform in-situ dimensional inspections at key points in the machining cycle. Data is fed back in real-time to the CNC control system, triggering compensation commands to correct subsequent tool paths, forming a closed-loop control chain of "machining-measurement-compensation." This mechanism transforms post-process inspection into process control, significantly improving the first-piece success rate and batch consistency of critical dimensions such as flatness, parallelism, and hole diameter precision.
Value Realization: Empowering Chip Innovation and Iteration
The in-depth application of precision CNC machining capabilities in the chip industry goes far beyond the manufacturing of individual components:
-
Accelerating R&D Cycles: Rapidly responding to prototype design iterations, significantly compressing the R&D cycle for complex precision components.
-
Ensuring Mass Production Reliability: Providing core components with nanometer-level dimensional stability for advanced process equipment (such as precision components inside EUV lithography machines) and high-performance chip cooling solutions, ensuring long-term operational precision of the equipment.
-
Breaking Physical Limits: Continuously pushing the boundaries of chip packaging density and cooling efficiency, providing a solid physical foundation for the next generation of higher computing power and lower power consumption chip architectures.
Precision Knows No Bounds
As chip technology continues to evolve towards smaller nanometer nodes, higher integration, and stronger computing power, the performance requirements for the precision metal components that support their manufacturing will inevitably increase. As the core driving unit of the precision manufacturing architecture, the dynamic evolution of the CNC technology system has never stopped. Its evolutionary path presents a distinct multi-dimensional integration feature: continuous refinement of nano-scale motion control capabilities, real-time process decision-making modules empowered by artificial intelligence algorithms, and continuous expansion of the processability boundaries of emerging materials. This deep synergy goes beyond simple technological superposition and is driving the reconstruction process of physical limits in the field of micro-machining. Its significance transcends the achievements within the scope of mechanical engineering and lies in building the underlying capability base that supports the continuous exploration of the micro-world in digital civilization. Each seemingly minor process precision iteration (such as breakthrough optimization of micron-level tolerances) is actually accumulating potential energy for subsequent paradigm shifts in chip architecture.