Silent Precision Revolution: When CNC and Special Welding Reshape the DNA of Data Center Cooling
At the core of data center liquid cooling systems, the Cooling Distribution Unit (CDU) functions like a precisely operating heart. Within the metal chamber through which thousands of liters of coolant flow per minute, a deviation in the flow channel width that is less than the diameter of a human hair can lead to a 15% reduction in system efficiency. A micro-porosity in a weld seam may potentially cause a catastrophic leak three years later—these challenges are the touchstones of modern manufacturing processes.
Five-axis CNC technology is redefining the way CDUs are born. As a block of 316L stainless steel is machined, a micrometer-level dynamic compensation system continuously corrects the tool path. This is not mere "sculpting," but rather topological optimization based on fluid simulation data: creating a mirror-like flow channel with a surface roughness of Ra0.4μm in high-pressure turbulent areas, and maintaining a coplanarity of ±0.01mm at flange mating surfaces. Ultimately, each manifold becomes a work of art that conforms to fluid dynamics. The value of this precision is directly translated into reduced coolant pumping power consumption—data from ASHRAE laboratories shows that optimized flow channels can improve system efficiency by 17%.
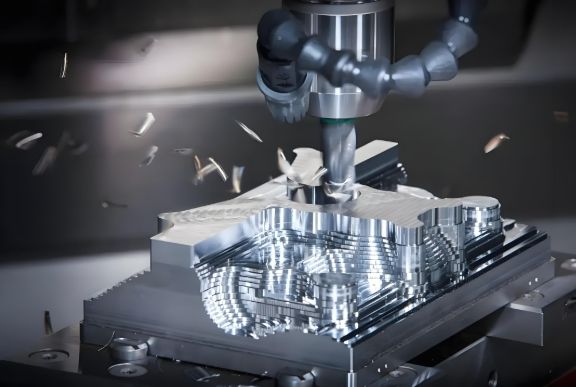
However, perfect parts are only the beginning. When multiple stainless steel components are assembled, thermal deformation from traditional welding can destroy the precision machining results achieved earlier. Thus, vacuum brazing technology takes the stage: in a vacuum environment thinner than the surface of the moon (10⁻⁴Pa), copper-based solder seeps into the interstitial spaces of the stacked metals like capillaries. Molecular-level bonding creates dense weld seams with a porosity rate of less than 0.3%, allowing the heat exchanger unit to withstand a water hammer impact of 8MPa—equivalent to the pressure exerted by a parked SUV on a fingernail.
Addressing the long-standing challenge of dissimilar metal connections between copper and aluminum, friction stir welding demonstrates unique process advantages. Its 450℃ high-speed rotating probe induces plastic flow at the interface, prompting directional migration of aluminum and copper atoms in a solid-state environment. This metallurgical bonding based on dynamic recrystallization fundamentally avoids the brittle β-phase compounds produced by fusion welding, stabilizes electrical conductivity loss within a 5% threshold, and endows the joint with reliable performance to withstand extreme temperature cycling (-40℃ to 120℃).
When the fluid efficiency of mirror-like flow channels, the structural integrity of zero-defect weld seams, and the electrochemical tolerance of materials form a triple safeguard, the service life of the CDU breaks through the physical limits of traditional design. In salt spray laboratories, these components successfully pass a 3000-hour corrosion test; in actual data center operations, they support stable, maintenance-free operation for 15 years. The significance goes beyond mere part manufacturing—it is about compressing the failure probability of the cooling system to near zero through micrometer-level control and nanometer-level surface integrity.
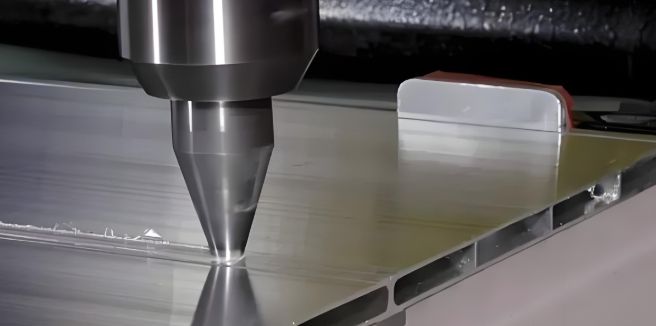
As cutting-edge liquid cooling technology drives the evolution of computing power, the real transformation often lies between the metal lattices. Those invisible precision flow channels, immeasurable residual stresses, and incalculable turbulent flow controls ultimately converge into the underlying logic of the stable operation of data centers. As thermal management becomes a necessity in the digital world, the manufacturing process revolution has quietly rewritten the rules of the game.