Precision Manufacturing in Liquid Cooling: The Silent Driver of Cold Plate Technology Evolution
The tide of liquid cooling systems in data centers is propelling server thermal management into uncharted waters. As chip power density breaks through physical limits, every component along the heat dissipation path becomes a critical chokepoint. Server liquid cooling cold plates, which directly contact the heat source, are like the nerve endings of the system. Their manufacturing precision and reliability directly determine the success or failure of the entire cooling chain. In this silent technological revolution, precision machining processes are redrawing the boundaries of performance.
Microchannels carved by five-axis联动CNC systems form the physical foundation of cold plate performance. These fluid channels, with widths close to the diameter of a human hair, require tool path errors to be controlled at a microscopic level. In a high-density computing cluster, an aluminum cold plate that has been in continuous operation for two years still maintains its initial geometric sharpness of the CNC-formed fin array, with pressure drop fluctuations kept within a negligible range. This stability stems from a deep understanding of material lattice structure and cutting mechanics, akin to a watchmaker's precise control of each process, like adjusting the hairspring.
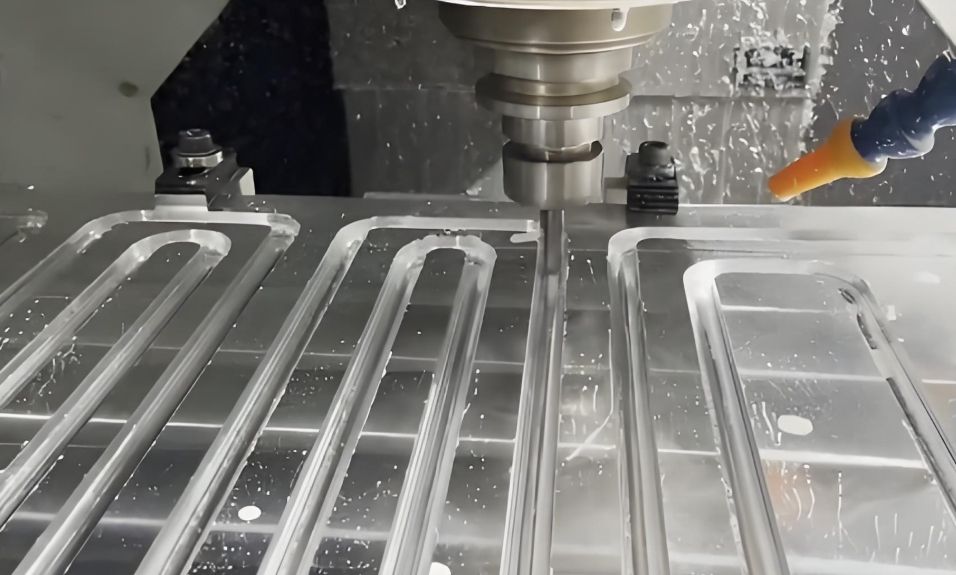
When cold plates need to integrate complex manifolds or connect to external circuits, the thermal shock of traditional welding becomes an invisible killer. Friction stir welding, through mechanical stirring and precise thermal management, allows metals to plastically intermingle in the solid state. After welding, the flatness of the stainless steel flow path is close to that of an optical mirror, and the heat-affected zone is reduced to one-tenth the width of traditional processes. This technology has enabled a certain immersion liquid cooling system to pass a hundred thousand thermal cycles test, with the sealing interface still maintaining molecular-level integrity.
Facing the dilemma of heterogeneous combination between copper alloy microchannels and special alloy casings, vacuum brazing demonstrates unique charm. Specialized filler metals build metallurgical bridges in submillimeter gaps, balancing the thermal expansion differences between materials while avoiding electrochemical corrosion pitfalls. A certain heterogeneous computing cold plate, through gradient temperature-controlled brazing, has significantly accelerated the efficiency of heat removal from the chip surface.
The real breakthrough comes from the co-evolution of the manufacturing process chain. As cold plate structures evolve towards three-dimensional topological forms: CNC machining creates fluid-dynamics-optimized curved cavities, friction stir welding achieves stress-free packaging of manifold interfaces, and brazing completes atomic-level bonding of heterogeneous interfaces. This integrated manufacturing solution has enabled a certain liquid-cooled server to achieve a coolant leakage rate that is stably better than aerospace hydraulic standards in extreme temperature difference tests.
As liquid cooling technology leaps from a supporting system to the core of computing infrastructure, cold plate manufacturing has entered a new era of precision engineering. We use CNC precision as the foundation, reshape connection logic with friction stir welding, and break through material barriers with brazing, providing a continuous flow of cooling blood for high-density computing.
Explore how precision manufacturing can inject certainty into the next generation of liquid cooling architecture:
www.simituo.com