High-Density Computing Heat Dissipation Core: Decoding the Manufacturing Process of Cooling Manifolds
Behind the continuous computing power released by server clusters, precision cooling systems play a vital role. The cooling manifold, as the core artery of the liquid cooling system, profoundly affects the reliability of the loop's operation. Under the harsh working conditions of continuous pulsating impacts from high-pressure fluid and periodic thermal oscillations, the manufacturing process must focus on millimeter-level dimensional accuracy and long-term durability to establish a solid baseline for performance.
Multi-axis CNC machines demonstrate their core value in the formation of complex manifolds. Through precision numerical control cutting, high-strength aluminum alloy or copper alloy blanks are transformed into three-dimensional structures with winding channels. The cross-sectional shape and surface texture of these internal flow channels significantly influence the fluid dynamics characteristics, typically requiring a surface roughness better than Ra 0.8 micrometers. The unique repeat positioning accuracy of the CNC process ensures that the geometric error of each product does not exceed 0.02 millimeters, while the flatness of the flange mating surfaces is controlled within a 0.05-millimeter threshold, creating the basic conditions for system sealing.
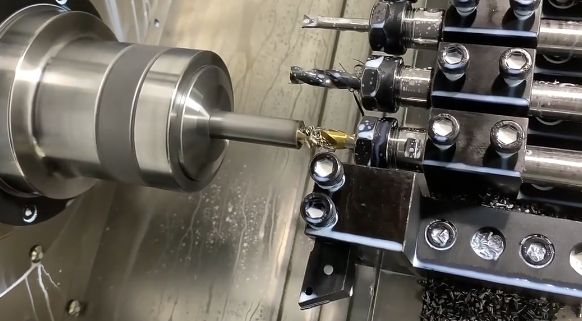
It is worth noting that monolithic manifolds often need to be processed in sections and then integrated. At this point, vacuum brazing shows unique advantages. In a sealed furnace chamber, special brazing filler metals capillary penetrate the gaps in the base materials. When the temperature precisely exceeds the solidus line of the material, the molten filler metal forms a metallurgical bond with the base material. This process avoids deformation in the heat-affected zone and maintains the dimensional stability of the original CNC machining.
The key value of the brazing process in manifold manufacturing is reflected in the following aspects:
-
Sealing Integrity: Continuous and uniform braze joints can withstand working pressures above 15 bar and repeated thermal shocks.
-
Structural Conformity: The heat input is only 30% of that of arc welding, with the base material deformation controlled within 0.1 millimeter.
-
Material Compatibility: Successfully applied to aluminum-copper dissimilar metal joints, solving the problem of different thermal expansion coefficients.
The quality verification system includes a multi-level inspection process. A 3D optical scanner captures deformations at the 0.005-millimeter level, the pressure decay method detects micro-leakages at the 10⁻³ mbar l/s level, and the helium mass spectrometer has a detection sensitivity at the 10⁻⁹ atm cc/sec level. It is worth noting that a batch of manifold products once passed a 2,000 thermal cycle test without any fatigue cracks appearing in the braze joint areas.
Currently, the penetration rate of liquid cooling in data centers has exceeded 20%, with the demand for precision manifolds growing by an average of 34% annually. The latest process breakthroughs have reduced the flow channel wall thickness to 1.2 millimeters, and combined with topological optimization design, the overall pressure drop has been reduced by 18%. Choosing a manufacturing partner that masters the core processes will provide sustainable cooling assurance for high-heat-density devices.To gain a deeper understanding of the manufacturing technology and engineering cases of high-reliability cooling manifolds, you can visit www.simituo.com to obtain the complete technical documentation and white papers on solutions.