CNC and Brazing: The Key Coupling in Aerospace Heat Sink Module Manufacturing
In the demanding environment of space, the efficient heat dissipation of electronic equipment is directly related to the success or failure of a mission. Spacecraft heat sink modules, like precision temperature regulation organs, bear the crucial responsibility of rapidly conducting and dissipating waste heat generated by key equipment. Faced with the extreme temperature differences, vacuum conditions, and strict weight limitations of space, the manufacturing process of these modules must pursue the utmost reliability and performance. In current technical solutions, the deep integration of CNC (Computer Numerical Control) machining and vacuum brazing has become the core process supporting the manufacturing of high-end heat sinks.
Precision Foundation: Configuration Freedom Enabled by CNC
The efficiency of heat sink modules hinges on their complex internal structures—microchannels, fin arrays, and heat pipe mounting slots, all of which directly impact thermal exchange efficiency and fluid dynamics. Traditional machining methods often fall short in this regard. The introduction of CNC technology has changed this situation. With high-rigidity equipment and precision cutting tools, CNC can achieve micrometer-level precision milling and cutting of three-dimensional complex structures in high thermal conductivity base materials such as aluminum alloy and copper. Whether it is the uniform distribution of ultra-thin fins, microchannel networks with extremely high aspect ratios, or installation surfaces that ensure perfect contact with devices (with planarity errors often needing to be ≤0.05mm), CNC machining can reliably achieve these requirements. This level of processing freedom is the prerequisite for realizing efficient heat dissipation topological designs.
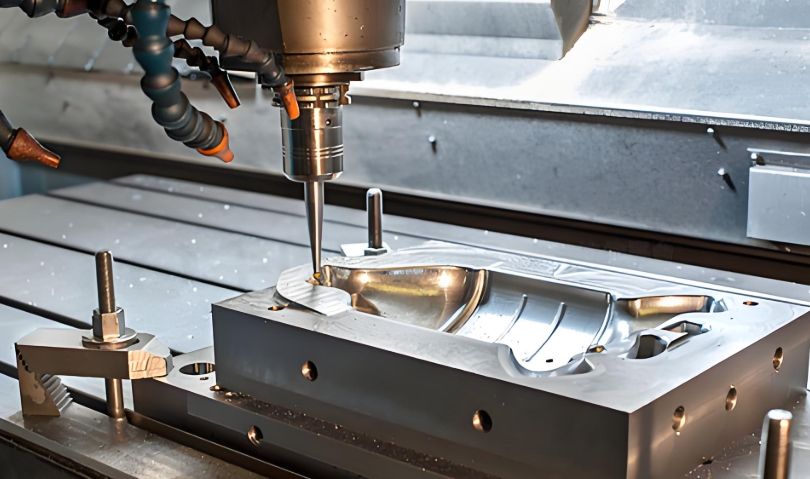
Seamless Connection: Reliable Integration through Vacuum Brazing
However, complex CNC components need to be reliably connected to form a fully functional heat sink module. Vacuum brazing technology plays a decisive role in this process. The process is carried out in a highly clean vacuum furnace, completely eliminating oxygen contamination. The core of vacuum brazing lies in its precise process control. The entire process needs to be conducted in a clean vacuum environment, completely isolating the influence of oxygen and other contaminants. The key point is: on the interface that has been precision-machined by CNC and pre-placed with special brazing filler (such as aluminum-silicon-based filler), a carefully designed and precisely controlled heat treatment procedure is applied. The magic here is that the metal base material itself does not melt, but relies on the capillary force of the molten filler to achieve the tight binding of metal atoms in the solid state. This binding method brings significant advantages: the heat-affected zone is very small, much smaller than conventional welding. Therefore, it can effectively avoid common problems such as base material deformation and material performance degradation, and is especially suitable for the delicate thin-walled structures and precision components in heat sink modules. The resulting joint is not only strong and has excellent sealing performance, but more importantly, it has extremely low thermal resistance. It is like building a smooth and unobstructed thermal bridge inside the heat sink module, ensuring the efficiency and integrity of the heat transfer path.
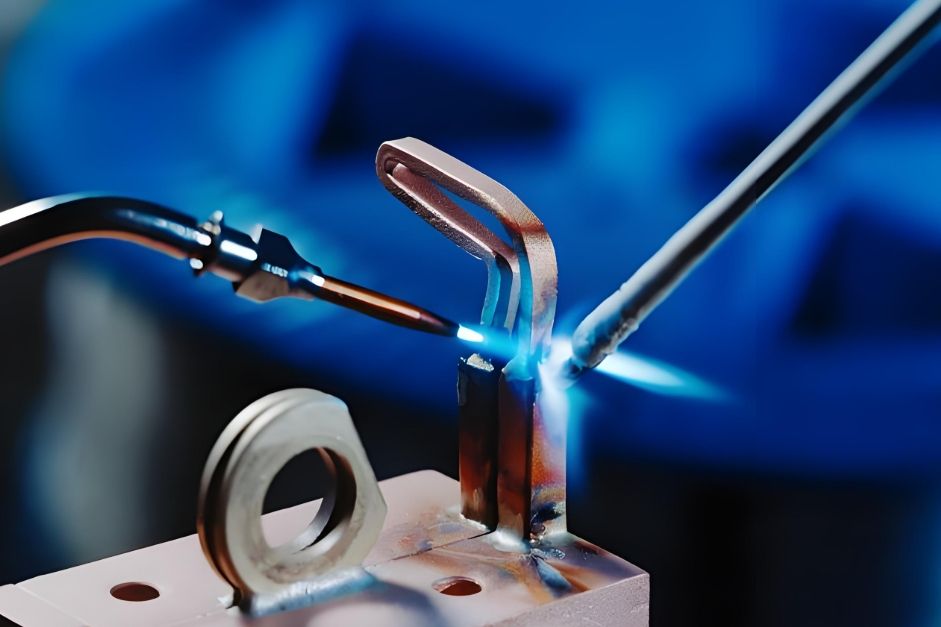
Coupling Process: Multiplied Efficiency
The integration of CNC and vacuum brazing is not a simple series connection. The key lies in the deep collaboration during the design phase. Engineers need to consider the manufacturability of CNC (such as tool accessibility and structural rigidity) and the process requirements of brazing (such as joint gap control and filler placement) from the very beginning of the heat sink module configuration design. For example, in manufacturing the main body of a certain type of spacecraft heat sink, CNC precision machining produces an aluminum alloy base plate with complex internal flow paths and mounting platforms, as well as multi-layer fin arrays, with all brazing interfaces having precise gaps reserved. Subsequently, after strict cleaning, precise assembly, and pre-placing of filler, the components enter the vacuum brazing furnace to complete the one-time overall connection under a precise temperature control curve. This seamless process significantly improves yield and structural consistency.
Tests have shown that aerospace heat sink modules manufactured through the integration of CNC precision machining and vacuum brazing have significantly higher thermal conduction efficiency, structural strength, and long-term reliability under thermal cycling compared to products made with traditional processes. In rigorous simulated space environment validation, they demonstrate excellent performance stability, fully meeting the spacecraft's stringent requirements for lightweight and highly reliable heat dissipation.
The deep coupling of CNC machining and vacuum brazing represents the cutting-edge direction in the manufacturing of high-end heat sink modules. It integrates the freedom of design, the precision of forming, and the reliability of connection into one process, providing a key technological pathway to break through heat dissipation bottlenecks for spacecraft and other cutting-edge fields. This collaborative innovation will continue to drive thermal management technology towards more efficient, compact, and reliable directions.